Roofing Systems
Board Insulations
The most common “Board Insulations” used on flat and low-sloped roof structures are Expanded Polystyrene, Extruded Polystyrene, PolyISOcyanurate, Wood Fiber, Perlite & Gypsum. Board Insulations provide roofing systems with thermal resistance value, board insulations protect the roofing membrane by acting as a separator from a structure’s rough surface; or, in re-roofing the board may act as a new base for a new roofing membrane (re-cover). Board Insulation can also be tapered to provide slope to buildings with dead level roofing surfaces; ponding water on a roof holds potential for leaks; water removed from the building by sloped roof surfaces no longer pose a threat.
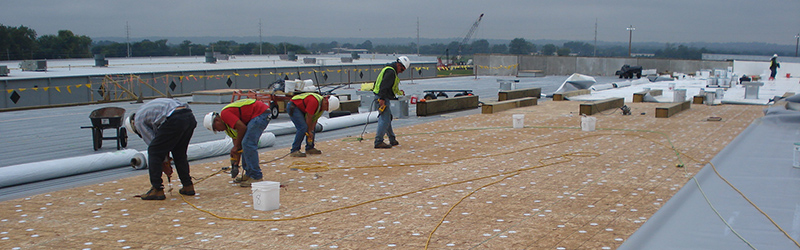
EPS (Expanded Polystyrene) is a typically inexpensive board insulation that can also be tapered to achieve roof slope on flat roof decks. When used as a insulator, its R-value per inch, per cost, is rated low. EPS is offered in different densities. A higher rated density (less air in the product) will allow for the product to hold up under greater pressure, reducing its compaction (destruction) from roof traffic, however, EPS is not recommend for any type of regular pedestrian roof traffic without adding a rigid cover-board or walkway pavers to disperse the weight over a larger area. EPS in most cases cannot be adhered to directly. EPS is highly flammable and needs to be treated or sandwiched between other fire resistant products to achieve a fire resistance classification or rating. EPS is not water-resistant and will retain moisture. EPS has the capability to be recycled.
Extruded Polystyrene can be used as board insulation or tapered board roof insulation. When used as insulator, its R-value per inch is good, its cost per inch is fair. Extruded is flammable and like EPS must be sandwiched between other class “A” products to achieve any type of a fire rating. What sets Extruded apart from other insulation boards is it has a tight closed cell structure (less air) that gives it a high compressive strength and a high moisture resistants’. Extruded comes in different densities and is excellent when used under heavy loads to support roofing systems from compacting. Like EPS, Extruded in most cases cannot be adhered to directly; it generally is mechanically fastened with a coverboard in fully adhered applications.
ISO (PolyISOcyanurate) has many uses in roofing systems. When used as insulation board, its R-value per inch, per cost, is highly rated. ISO board insulation can be tapered to provide slope to flat roof decks. ISO is fire-resistant. ISO will hold up to light pedestrian traffic, but is not water-resistant, it will retain moisture. ISO when used in its 2-part liquid form can be used as an adhesive to adhere roofing systems together, as well as, a spray to fill voids or cracks as an insulator.
Coverboards are generally thin boards that are rigid and often water & fire resistant. Rigid coverboards can be used to protect the roofing system’s other layer(s) of insulation board(s) below it from being crushed by pedestrian foot traffic. Coverboards on re-roofing re-covers are used to protect the new roofing membrane by separating it from the pre-existing roofing, in this case this coverboard provides a new viable surface on to which the new membrane can sit (adhered or looselaid). Coverboards are also added to a roofing system to provide a fire-resistant sheet which aids in protecting the building from fire entering from above the roof’s surface. Coverboards provide a surface onto which a membrane can be adhered or applied when the board insulation below it isn’t suitable to accept such applications, such as adhesives or hot asphalt that break down foam boards. Plywood, Fiberboard (wood fibers), Perlite (expanded rock), Densdeck (gypsum), and recently high density ISO boards are a few examples of commonly used coverboards.
Extruded Polystyrene can be used as board insulation or tapered board roof insulation. When used as insulator, its R-value per inch is good, its cost per inch is fair. Extruded is flammable and like EPS must be sandwiched between other class “A” products to achieve any type of a fire rating. What sets Extruded apart from other insulation boards is it has a tight closed cell structure (less air) that gives it a high compressive strength and a high moisture resistants’. Extruded comes in different densities and is excellent when used under heavy loads to support roofing systems from compacting. Like EPS, Extruded in most cases cannot be adhered to directly; it generally is mechanically fastened with a coverboard in fully adhered applications.
ISO (PolyISOcyanurate) has many uses in roofing systems. When used as insulation board, its R-value per inch, per cost, is highly rated. ISO board insulation can be tapered to provide slope to flat roof decks. ISO is fire-resistant. ISO will hold up to light pedestrian traffic, but is not water-resistant, it will retain moisture. ISO when used in its 2-part liquid form can be used as an adhesive to adhere roofing systems together, as well as, a spray to fill voids or cracks as an insulator.
Coverboards are generally thin boards that are rigid and often water & fire resistant. Rigid coverboards can be used to protect the roofing system’s other layer(s) of insulation board(s) below it from being crushed by pedestrian foot traffic. Coverboards on re-roofing re-covers are used to protect the new roofing membrane by separating it from the pre-existing roofing, in this case this coverboard provides a new viable surface on to which the new membrane can sit (adhered or looselaid). Coverboards are also added to a roofing system to provide a fire-resistant sheet which aids in protecting the building from fire entering from above the roof’s surface. Coverboards provide a surface onto which a membrane can be adhered or applied when the board insulation below it isn’t suitable to accept such applications, such as adhesives or hot asphalt that break down foam boards. Plywood, Fiberboard (wood fibers), Perlite (expanded rock), Densdeck (gypsum), and recently high density ISO boards are a few examples of commonly used coverboards.
Single-Ply Membrane Roofing
Single Ply Membrane Roofing (low-slope applications) provides excellent detailing components for roofs with many penetrations. They have the versatility for quality tie-ins to different surfacing, odd shapes, and when fully adhered they all share excellent finish coverings for vertical applications (walls):
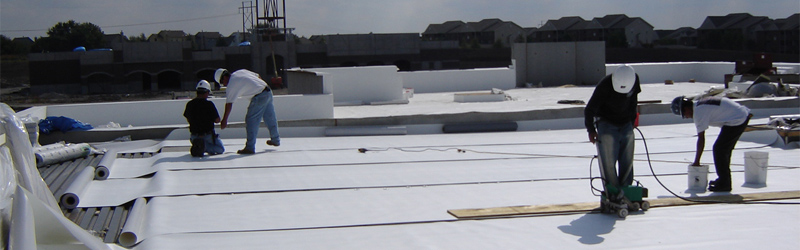
Types
EPDM (Ethylene Propylene Diene Monomer), also known as rubber, provides excellent weathering characteristics, EPDM is durable, and because of its ability to stretch and maintain that resilience over time, EPDM alone has the highest capacity to resist hail damage more than any other of the single ply membranes. EPDM membranes and their components are adhered together with adhesives and tapes. EPDM membrane offers qualities which allows for easy maintenance giving your roof a chance to be serviced well into the future having been installed under the right conditions. EPDM, traditionally black in color, is now offered in white as well. EPDM is manufactured in different membrane thicknesses.
TPO (Thermoplastic Polyolefin) & PVC (Polyvinyl-chloride), also known as plastics, come in light colors (white, tan, gray) and are called cool roofs for their ability to reflect sunlight, reducing the roof’s temperature, thereby reducing air conditioning costs. TPO membrane and its components are held together by using a combination of adhesives and heat welding. PVC membrane and its components are heat welded together. When supported by rigid coverboards plastics have greater hail resistant qualities. Both plastics (TPO & PVC) come in different membrane thicknesses.
TPO (Thermoplastic Polyolefin) & PVC (Polyvinyl-chloride), also known as plastics, come in light colors (white, tan, gray) and are called cool roofs for their ability to reflect sunlight, reducing the roof’s temperature, thereby reducing air conditioning costs. TPO membrane and its components are held together by using a combination of adhesives and heat welding. PVC membrane and its components are heat welded together. When supported by rigid coverboards plastics have greater hail resistant qualities. Both plastics (TPO & PVC) come in different membrane thicknesses.
Attachments
Ballasted Roofing Systems rely on weight installed on top of the membrane to hold the membrane still and in place. In most cases rock (smooth river worn rock) is applied over the membrane to weight it down; however, ballast pavers and garden roofs operate under the same principles of gravity. Ballast is commonly called and or known as “overburden.” Rock ballasted roofing systems are seen as an attractive final surfacings and do offer some solar heat resistance. A ballasted roofing system (using rock) is - as a rule – less expensive than other roofing systems because of the natural abundance of rock in comparison to the higher cost of manufactured fasteners and adhesives that are used in other roofing system attachments. Although pavers can be installed for pedestrian traffic, ballasted roofing systems are not recommended for roofs with high pedestrian traffic, because the membrane is covered and cannot be easily viewed. Ballasted systems can be difficult to uncover leaks when they occur. The weight of the ballast can also be a concern; always consult an engineer to have your roof evaluated for weight restrictions.
Mechanically Fastened Roofing Systems rely on fasteners attaching the insulation as well as the single-ply membrane to the roof’s decking to secure it in place. Traditionally, the fasteners used to secure the membrane to the roof are installed in the seams (where the rolls overlap) of the roofing membrane; those seams are typically 8’ to 12’ apart (the width of the membrane roll) in the roof’s field; with half rolls (reducing the length between laps) installed at the roof’s perimeters for extra securing protection. Mechanically Fastened roofing systems are subjected to wind conditions which at times cause the membrane to flutter stressing the membrane at its attachment points. Recently, the insulation plates that are used with the fasteners to secure the board insulation to the roof deck, those insulation plates have been coated with the same plastic as the single-ply membrane’s plastic and the membrane is heat to those insulation plates from above with heated magnets. This checkering of the membrane’s points of attachment in the roof’s field, rather than the traditional 8’ to 12’ seam attachment, greatly reduces the distance between the membrane’s points of attachment which further reduces the membrane’s fluttering, which further reduces the stress on the membrane. Mechanical fastened systems are also considered a less expensive roofing system.
Adhered Roofing Systems rely on the substrate (the board insulation) being either mechanically fastened or adhered to the roof deck, then the single ply membrane or BUR is fully adhered (laminated) to that insulation/coverboard. For single ply membranes this method of attachment has two outstanding qualities; the membrane – should there be a leak – is easily inspected because there is no ballast/overburden between you and a visual inspection of that membrane; second, the membrane being completely adhered to the rigid board insulation and is not subject to high winds fluttering it about. Aided by walkway pads, walkway pavers, or a rigid coverboard (or a combination of more than one of them), pedestrian traffic can be managed in order to protect the roof from pedestrian traffic. A “Fully Adhered” single ply roofing membrane has several excellent qualities; and is considered a mid-ranged priced roofing system.
Mechanically Fastened Roofing Systems rely on fasteners attaching the insulation as well as the single-ply membrane to the roof’s decking to secure it in place. Traditionally, the fasteners used to secure the membrane to the roof are installed in the seams (where the rolls overlap) of the roofing membrane; those seams are typically 8’ to 12’ apart (the width of the membrane roll) in the roof’s field; with half rolls (reducing the length between laps) installed at the roof’s perimeters for extra securing protection. Mechanically Fastened roofing systems are subjected to wind conditions which at times cause the membrane to flutter stressing the membrane at its attachment points. Recently, the insulation plates that are used with the fasteners to secure the board insulation to the roof deck, those insulation plates have been coated with the same plastic as the single-ply membrane’s plastic and the membrane is heat to those insulation plates from above with heated magnets. This checkering of the membrane’s points of attachment in the roof’s field, rather than the traditional 8’ to 12’ seam attachment, greatly reduces the distance between the membrane’s points of attachment which further reduces the membrane’s fluttering, which further reduces the stress on the membrane. Mechanical fastened systems are also considered a less expensive roofing system.
Adhered Roofing Systems rely on the substrate (the board insulation) being either mechanically fastened or adhered to the roof deck, then the single ply membrane or BUR is fully adhered (laminated) to that insulation/coverboard. For single ply membranes this method of attachment has two outstanding qualities; the membrane – should there be a leak – is easily inspected because there is no ballast/overburden between you and a visual inspection of that membrane; second, the membrane being completely adhered to the rigid board insulation and is not subject to high winds fluttering it about. Aided by walkway pads, walkway pavers, or a rigid coverboard (or a combination of more than one of them), pedestrian traffic can be managed in order to protect the roof from pedestrian traffic. A “Fully Adhered” single ply roofing membrane has several excellent qualities; and is considered a mid-ranged priced roofing system.
Built-Up-Roofing (BUR)
BURs are the toughest of the roofing systems. Where pedestrian traffic is high, a BUR roof system has no equal. A BUR roofing membrane is constructed on the roof by combining layers of materials (roll goods) together and in their total they act as the roofing membrane. In the matrix of a traditional BUR membrane, tar or asphalt act as not only the glue which binds or adheres together the three to four layers of sheet-fabric roll goods, but that very tar or asphalt also acts as the main waterproofing component/ingredient which is being held/contained in place by those three to four layers of sheet-fabric. In a traditional BUR, tar or asphalt is the heart of the final waterproofing membrane. Hot tar (also known as pitch) has been virtually replaced by hot asphalt, but hot tar remains an outstanding product because of its ability – after it has been installed – to easily melt and flow into voids giving it its title “self-mending.”

Modified BUR - In the last thirty years, traditional BURs have been somewhat replaced by new high-bred membranes called “Modified Roofing Sheets.” These modified sheets (roll goods) don’t rely solely on tar or asphalt to be the heart of the membrane; the new sheets are themselves a manufactured complete preassembled waterproofing membrane. Modified sheets are made by modern formulations that include rubber as well as asphalt materials held together with fabric now called scrim. Two layers of these modified sheets can provide an excellent finished roofing membrane. Layers of modified sheets can be bound/adhered together by using hot asphalt, by fully torching them together with open flames, with cold adhesives, with cold adhesives that have their side laps torched or heat welded, or some modified sheets come complete as self-adhering sheets. These sheets are commonly put down in two layers. Sub layers are known as base-sheets, with the top layer or the finishing layer, being known as the cap-sheet. Capsheets can have a smooth finish and will need a final surfacing, or some come with a prefinished granule exterior. Two layers are common, three layers form an extremely rigid, tough, durable roofing membrane, or modified sheets can be combined with traditional BUR layer(s) in many different layer configurations, with many different schools of thought as to why. Modified roofing systems are excellent for their durability and are considered a more costly roofing membrane / system.
The Final Surfacing of a BUR is evolving as are the roll goods themselves. Gravel set in a pouring of tar or asphalt has been as traditional as any finished roofing surface. Gravel gives the BUR membrane a heavy, durable, attractive final surfacing that does offer some solar heat resistance, its extremely durable and holds up to foot traffic, hail and other weather conditions. A good quality aluminum coating locks in the BUR’s oils, and reflects solar heat adding years to your BUR if maintained. Then there is a whole new world of highly formulated coatings beginning to emerge as the final surfacing of BUR & single ply roofing systems; time will tell as to which one of them performs best. Coatings are generally considered a maintenance item, meaning coatings can wear and need to be redone. The final surfacing should act as a seal to keep the oils in the roofing system so the system can remain resilient, as well as designed to protect the membrane from pedestrian traffic when a good BUR roofing system is the only roofing system tough enough to stand up to the pressure of constant pedestrian traffic.
The Final Surfacing of a BUR is evolving as are the roll goods themselves. Gravel set in a pouring of tar or asphalt has been as traditional as any finished roofing surface. Gravel gives the BUR membrane a heavy, durable, attractive final surfacing that does offer some solar heat resistance, its extremely durable and holds up to foot traffic, hail and other weather conditions. A good quality aluminum coating locks in the BUR’s oils, and reflects solar heat adding years to your BUR if maintained. Then there is a whole new world of highly formulated coatings beginning to emerge as the final surfacing of BUR & single ply roofing systems; time will tell as to which one of them performs best. Coatings are generally considered a maintenance item, meaning coatings can wear and need to be redone. The final surfacing should act as a seal to keep the oils in the roofing system so the system can remain resilient, as well as designed to protect the membrane from pedestrian traffic when a good BUR roofing system is the only roofing system tough enough to stand up to the pressure of constant pedestrian traffic.
Green Roofing
Cool Roofs have been green roofing’s biggest step forward in the area of solar reflectivity which reduces radiant heating. Cities like Atlanta are known as “heat islands” because of the amount of radiant heat that the city absorbs from the sun. In roofing, the final surfacing has everything to do with absorbing or reflecting the sun’s rays. White TPOs and PVCs have increased their market share significantly because of their reflective quality, and have become known as “Cool Roofs.”
For a BUR, a final coat of a good quality “Aluminizer” not only offers excellent reflection of the sun’s rays, but also reduces the depletion of oil from the system’s membrane, extending the life of the roof.
For a BUR, a final coat of a good quality “Aluminizer” not only offers excellent reflection of the sun’s rays, but also reduces the depletion of oil from the system’s membrane, extending the life of the roof.
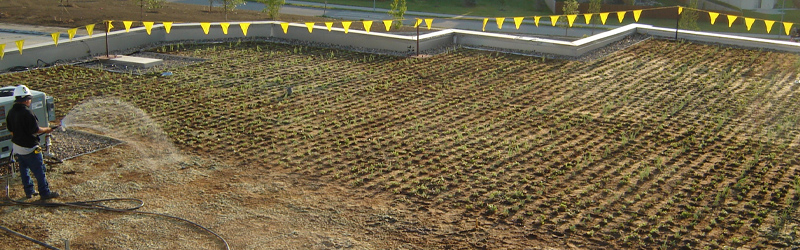
Garden Roofs offer several environmentally helpful and safe qualities. Garden roofs reduce heat absorption and they reduce water run-off. In cities where water run-off can turn into flash flooding because of the massive amounts of hard surface areas (parking lots, large buildings, and streets), garden roofs help replace the building’s hard surface with a roof that absorbs precipitation. One of the more impressive benefits to a garden roof is the water run-off that does occur has been tested and been found to be less toxic, carrying fewer pollutants than what drains from traditional roofs, proving to be much better for the environment. Garden roofs need special layers of materials to protect the roof membrane. Root barriers, drainage and retainage mats, as well as filter fabrics help protect the roof as well as the roof’s drains or gutters by containing the soil and plants.
“Extensive” garden roofs have a soil depth (media or medium) of no greater than approximately 5-inches; anything above 5-inches in depth is called an “Intensive” roof garden. Tray systems coming in different sizes (2’ x 2’, 2’ x 4’ as well as others) typically 4-inches deep, complete with all the components necessary for a garden roof are installed side by side with the thought that should you ever have problems with your roof you can remove the trays more easily to inspect the roofing. Most importantly, a properly design roof garden must have a quality roofing system under it. The garden means nothing if you’re tearing it up while trying to find leaks. Allow your roofing contractor to oversee the garden portion of your garden roof, or oversee your garden contractor to insure the roof is protected at all times and you’ll have your priorities in their proper place. Differing designs of Garden Roofs are as endless as the weight your building can support. The type of green roofing right for your roof depends on the weight load that your structure is rated for. Always consult a professional engineer if you are unaware of your structures limitations before beginning design.
“Extensive” garden roofs have a soil depth (media or medium) of no greater than approximately 5-inches; anything above 5-inches in depth is called an “Intensive” roof garden. Tray systems coming in different sizes (2’ x 2’, 2’ x 4’ as well as others) typically 4-inches deep, complete with all the components necessary for a garden roof are installed side by side with the thought that should you ever have problems with your roof you can remove the trays more easily to inspect the roofing. Most importantly, a properly design roof garden must have a quality roofing system under it. The garden means nothing if you’re tearing it up while trying to find leaks. Allow your roofing contractor to oversee the garden portion of your garden roof, or oversee your garden contractor to insure the roof is protected at all times and you’ll have your priorities in their proper place. Differing designs of Garden Roofs are as endless as the weight your building can support. The type of green roofing right for your roof depends on the weight load that your structure is rated for. Always consult a professional engineer if you are unaware of your structures limitations before beginning design.
Steep Slope Roofing
Underlayments - Whether it an asphalt shingle or a ceramic tile, shingles, slate and tile applications are shedding systems not waterproofing systems. All the pieces of a shingle roof are installed in an overlapping method to shed water from one piece on to the other until the water is off of your structure. A good underlayment is as important to a good roofing system as is the final surfacing be it a shingle or a tile, and in some circumstances such as a wood shingle or shake application, even more important.
Ice and watershield underlayments are waterproofing membranes used in critical areas of your roof such as the eaves, valleys and sidewalls where damning can occur. The damning of water caused from downpours, or ice buildup causes the draining water to start moving laterally, working against the side laps of the roofing units and in the case of freezing, water will and does start working up the slope because it collects from the bottom up. That is why at the gutter, or in the valley, in areas like these where water can damn a good underlayment is needed because when the water gets through the singles, it is the secondary source of protection for your structure.
Ice and watershield underlayments are waterproofing membranes used in critical areas of your roof such as the eaves, valleys and sidewalls where damning can occur. The damning of water caused from downpours, or ice buildup causes the draining water to start moving laterally, working against the side laps of the roofing units and in the case of freezing, water will and does start working up the slope because it collects from the bottom up. That is why at the gutter, or in the valley, in areas like these where water can damn a good underlayment is needed because when the water gets through the singles, it is the secondary source of protection for your structure.
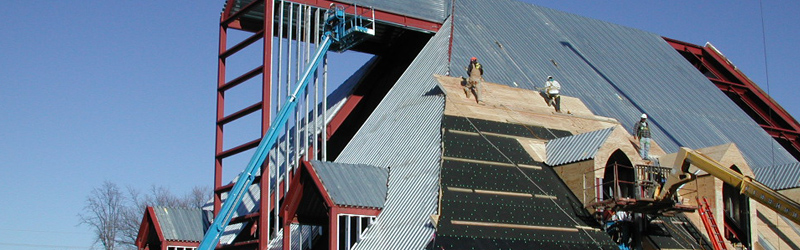
Asphalt Shingles are currently the most popular type of steep slope roof material because they are relatively inexpensive and are very simple to install. They come in a variety of colors and styles (weights), and are fairly durable and can be easily repaired and maintained.
A Slate Roof is one of the most durable roofing materials available. Slate used for roofing dates back to the twelfth century. Roofing Slate is a dense, sound rock, extremely tough and durable. Slates are heavy, starting at approximately 7-lbs per square foot for a ¼” slate, and depending on both the size and thickness can weigh up to 20-lbs per square foot for a 5/8” thick slate. Colors are given by the quarry they are mined from because that’s what the sediment’s mineral composition’s natural color was. Slate roofs have lasted a hundred years.
Interlocking Ceramic Tiles can last 75 to 100 years. Clay roof tiles date back 12 thousand years, made in Asia and the Middle East. Traditional tile roofing is made from fired clay. Factories are located where there is a natural abundance of this raw material. Clay fired tiles absorb almost no water which aids them against the freezing and thawing cycle. Tile roofs are heavy weighing between 6 to 18 pounds per square foot. Metal roofing that mimics tile may weigh as little as one pound per square foot.
Metal Roofing has dramatically increased its market share over the last 25 years because of the high performing finishes with typical 20-year warranties and the panel forming method which now conceals all fasteners adding to its esthetic qualities. Metal roofing is relatively light weight and like all water-shedding roofing systems requires a good underlayment, a high temperature underlayment. - Concrete and synthetic imitations are very abundant and great care needs to be taken when choosing an imitation product.
A Slate Roof is one of the most durable roofing materials available. Slate used for roofing dates back to the twelfth century. Roofing Slate is a dense, sound rock, extremely tough and durable. Slates are heavy, starting at approximately 7-lbs per square foot for a ¼” slate, and depending on both the size and thickness can weigh up to 20-lbs per square foot for a 5/8” thick slate. Colors are given by the quarry they are mined from because that’s what the sediment’s mineral composition’s natural color was. Slate roofs have lasted a hundred years.
Interlocking Ceramic Tiles can last 75 to 100 years. Clay roof tiles date back 12 thousand years, made in Asia and the Middle East. Traditional tile roofing is made from fired clay. Factories are located where there is a natural abundance of this raw material. Clay fired tiles absorb almost no water which aids them against the freezing and thawing cycle. Tile roofs are heavy weighing between 6 to 18 pounds per square foot. Metal roofing that mimics tile may weigh as little as one pound per square foot.
Metal Roofing has dramatically increased its market share over the last 25 years because of the high performing finishes with typical 20-year warranties and the panel forming method which now conceals all fasteners adding to its esthetic qualities. Metal roofing is relatively light weight and like all water-shedding roofing systems requires a good underlayment, a high temperature underlayment. - Concrete and synthetic imitations are very abundant and great care needs to be taken when choosing an imitation product.
Roof Terraces
Roof Terraces and Roof Gardens have become one of the new 'Eco-Friendly' options for your flat roof. Over the last ten years roof terraces have increased in both frequency and complexity. Contemporary Terrace designs can incorporate Urban Rooftop Gardens within the Terraces utilizing low maintenance plants, bushes, and trees.
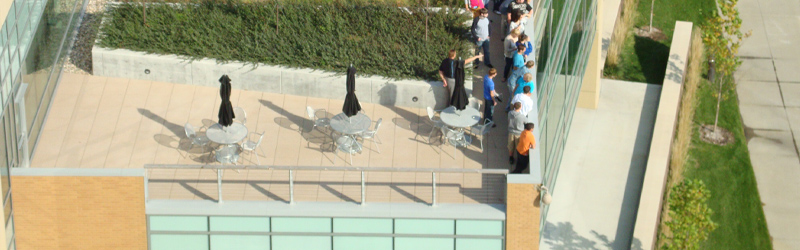
These Terraces can be used to create additional 'Living Spaces' ideal for entertaining or just a peaceful and relaxing lounging area. Terraces can also be used as an 'Employee Break Area, a personal 'Sundeck', or to just enjoy the view and overlook your surroundings. Whether you are in an Urban, Suburban, or Waterfront enviornment you can create the environment you desire and utilize your real estate that is often 'Out of Sight-Out of Mind'.
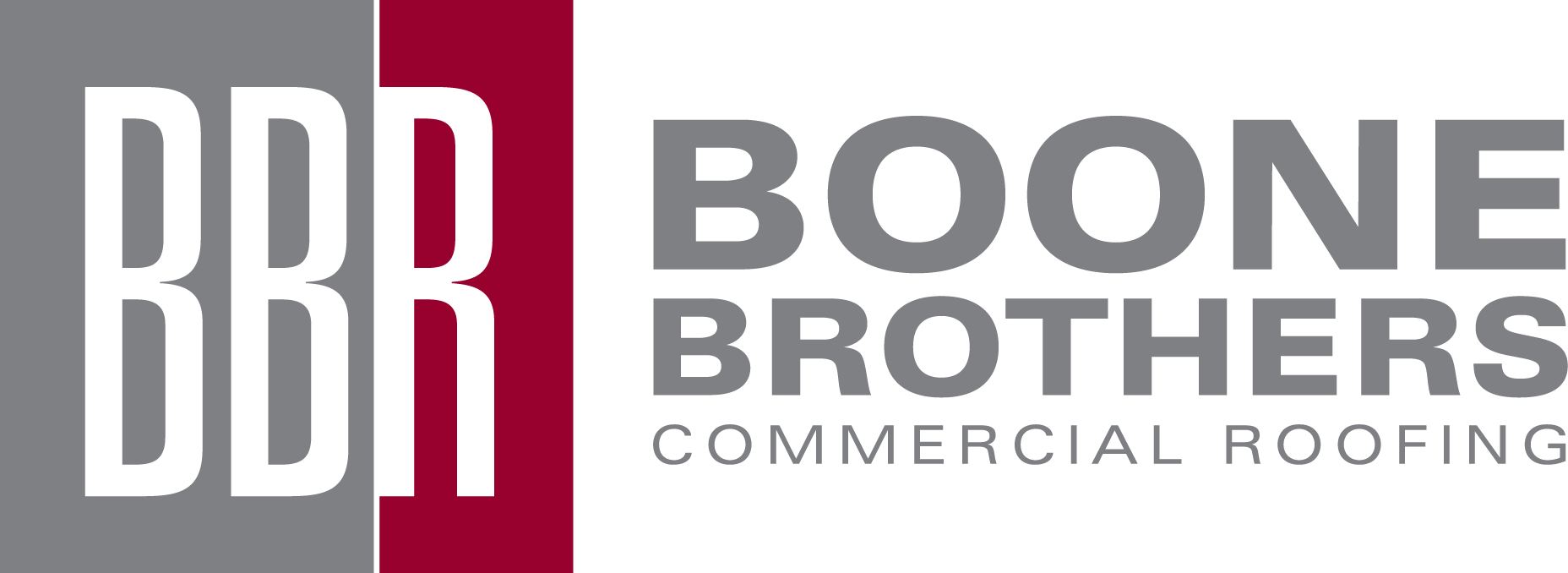